ADAMA praised for high-load, low-impact products
FOR many growers, they only need to look at their stack of used chemical containers in a season to understand how this extrapolates on a global scale and the volume of manufacturing, plastic, transport and handling required and its environmental impact.
The Australian team of one of the world’s major crop protection suppliers, ADAMA, decided to do something about this and is leading the way within the company and for the industry.
It commenced the development of higher-loading, or concentrated, formulations of various products in its stable more than 10 years ago to reduce the requirements and impact. Today, these formulations comprise about 30 per cent of its total volume in Australia.
ADAMA Australia has 26 high-load brands, positioning the company as the global leader in this technology. It is expecting another 12 high-load formulations to emerge from across its product portfolio over the next five years.
The Australian team’s high-load project was celebrated at a global awards presentation by the company earlier this year in Israel. It has taken little time for other country teams to follow the pathway.
It has become a sharp focus for countries like Brazil, the US and particularly Europe, where stringent plastic use regulations exist.
Stuart Moncrieff, General Manager - Marketing with ADAMA Australia, said the local team recognised amid the increasing environmental impact that it was their responsibility to help reduce it.
“As a global crop protection leader supplying more than 300 active ingredients and 1450 formulations, it is our responsibility to implement all available measures to reduce our environmental impact,’’ Stuart said.
This impact has been clearly outlined in recent years by the Food and Agriculture Organisation (FAO) and CropLife, which monitors data from container management schemes in almost 60 countries.
In 2018, the FAO reported that 12.8 million tonnes of plastic was used annually to produce, transport and store agricultural products.
In 2019, CropLife reported globally that at least 330,000 tonnes of crop protection packaging, including non-plastic packaging, was put into the market.
Globally, only 30 per cent of empty drums make it to recycling, whilst greenhouse gas emissions from the manufacture, transport and end-of-life disposal of agriculture plastics account for 3.5 per cent of annual emissions, expected to double by 2050.
Photo: According to CropLife, globally only 30 per cent of empty drums make it to recycling, whilst greenhouse gas emissions from the manufacture, transport and end-of-life disposal of agriculture plastics account for 3.5 per cent of annual emissions – and this is expected to double by 2050
Stuart said over the last three years, ADAMA Australia’s high-load project had reduced product volumes by a significant 10.8 million litres, also with less use of solvents and other formulation components, all of which equated to extensive benefits, including:
- 1 million fewer 10L drums and caps.
- 3 million fewer labels.
- 541 fewer trucks on the road.
- 32,000 fewer pallets.
- Reduced handling and exposure for retail partners and growers.
In terms of the environmental impact, this amounted to the following:
- 780,000 kilograms less plastic.
- 542 tonnes less truck greenhouse gas emissions per 1000 kilometres.
- 1.2 million kilograms less timber for pallets.
- A significant reduction in manufacturing emissions and sea freight.
He said the reduced volume had lowered the company’s energy and water consumption, plus reduced the amount of waste requiring management.
The high-load products undergo rigorous testing in-field, including performance in mixtures with other crop protection products and assessing their stability in storage. “We don’t just high-load products for the sake of it. We must ensure the field and user experience is not compromised,’’ Stuart said.
ADAMA Australia’s high-load product development also explores adding product use patterns during the process to provide additional benefits to growers. Any cost savings are reinvested into its future pipeline of products for the industry.
Stuart said the high-load products require an adjustment in application rates for growers and their advisors. ADAMA Australia, in some instances, changed the packaging and colour of various high-load formulations for easy differentiation from the original products.
Steve Scott, Country Manager ADAMA Australia, said the Australian network of rural suppliers and farmers strongly recognised the benefits of reduced freight, storage and handling, and also in consideration of the sustainability pressures facing the industry. “The high-load project is a win for all, the Australian rural supply network, farmers, ADAMA and the environment,” Steve said.
Photo: WA grower Darryl Sims, Beverley, says the more high-load crop protection products he can use, the better. “I end up with fewer drums in my chemical shed that I have to store, and I can keep things more neatly arranged and understand what products I have got,’’ he says.
Western Australian grower Darryl Sims, Beverley, said every farmer knew empty drums were the bane of their existence. “Whether I’m carting it, or my reseller is, it’s all got to fit in a truck, and the mountain of drums have to be cleaned at the end and then transported back for recycling,’’ Darryl said.
“The more high-load product I use, the better off I am. I end up with fewer drums in my chemical shed that I have to store, and I can keep things more neatly arranged and understand what products I have got.’’
Tim Gainsford, an irrigation and dryland farmer at Narromine in the Central West region of New South Wales, said that with the high-load products, “each container goes a lot further, which makes a lot of sense’’.
“It really reduces the amount of packaging you have to handle and dispose of after its use,’’ Tim said.
“From an environmental perspective, reducing the number of containers we are using each year also helps reduce our impact.’’
Discover High Load Products
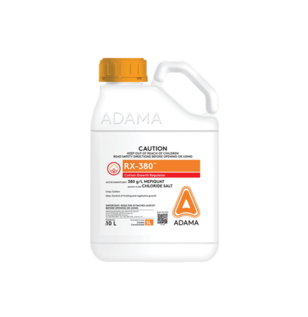
RX-380™
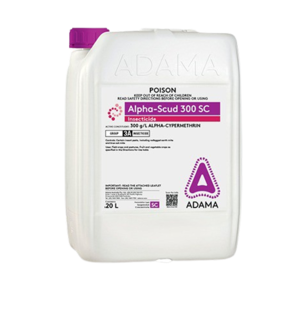
Alpha-Scud® 300
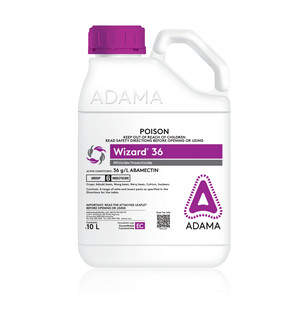