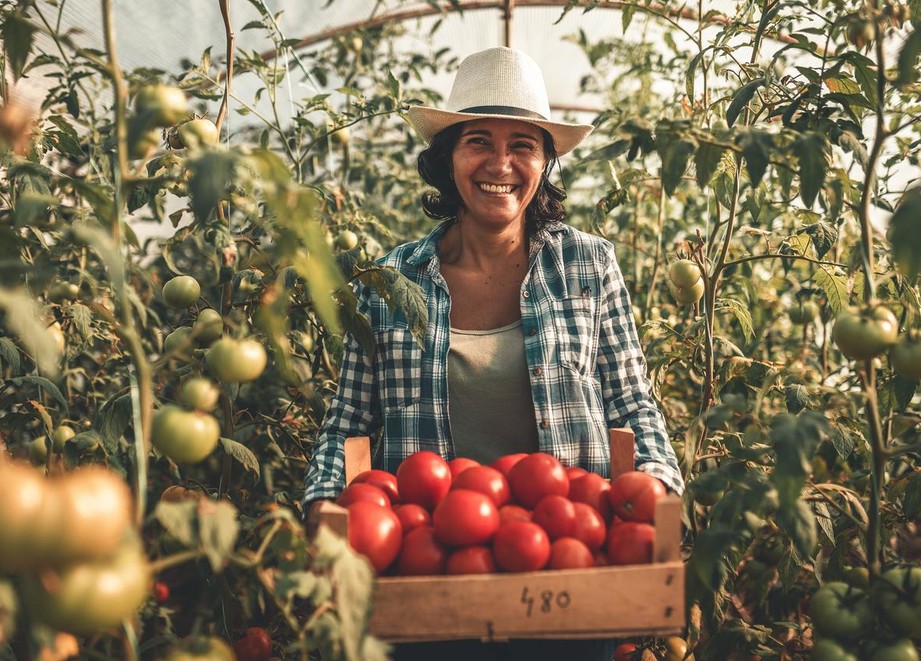
Our People
At ADAMA, we believe that everyone is entitled to a work environment that is both safe and healthy. To fulfill this commitment, we strive to proactively address health and safety risks, identify skill gaps, and promote a safe organizational culture. Our commitment to health and safety is formulated in the Global HSE policy and supported by the ADAMA Code of Conduct.
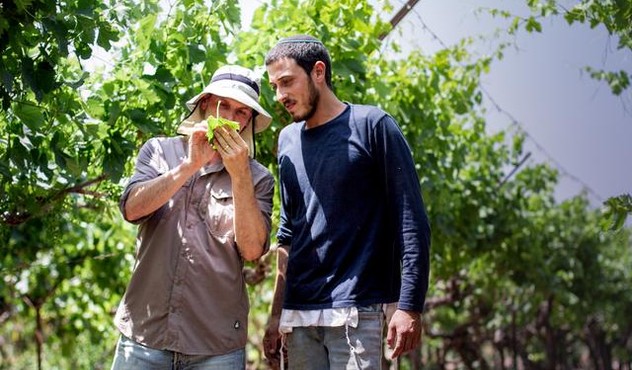
In accordance with our mission to better listen and learn, we actively involve employees in formulating initiatives to improve their safety and well-being. For example, we have regular meetings of employees and managers to discuss on ways to improve our performance. We also use our internal communication channels to invite employees to give us feedback and share suggestions for initiatives we should implement to improve our conduct in the field.
Another important means of employee involvement is our learning processes from actual events that are based on listening and learning from the employees themselves on ways for improvement and then, sharing insights gathered.
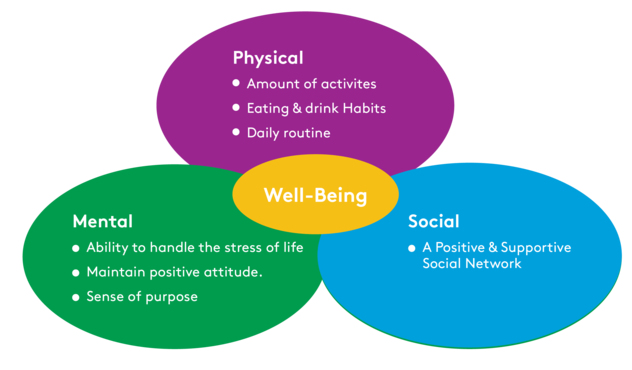
Some sites have a dedicated program on the subject, such as the wellbeing program we conducted in India last year. This particular site employs close to 500 people and therefore, safety is of paramount importance. Accordingly, we have formulated a proactive plan that expands our efforts to promote employee health and safety in the context of the employee experience – focusing on empowerment, enablement, and engagement. Various safety infrastructural processes were implemented alongside new initiatives that deal with a variety of issues such as: Physical & Mental Health; Safety Culture Development; Job Responsibility Design; Fun at the Workplace; and more.
The program includes training sessions, periodic inspections, thematic happenings, safety competitions, and gamification to ensure employee involvement. We are proud to share that the program is a success and shows a consistent increase each year in employee engagement, one of the main objectives of the program.
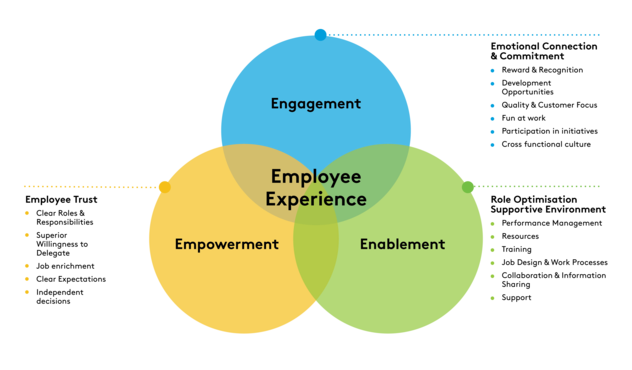
“Our employees are our top priority and therefore, we are committed to investing everything necessary to ensure their health and safety. We work in accordance with a clear and systematic plan, based on global standards, to ensure compliance with the zero-accident target."
Yossi Kronman
Former Head of HSE Standard & Operation Excellence
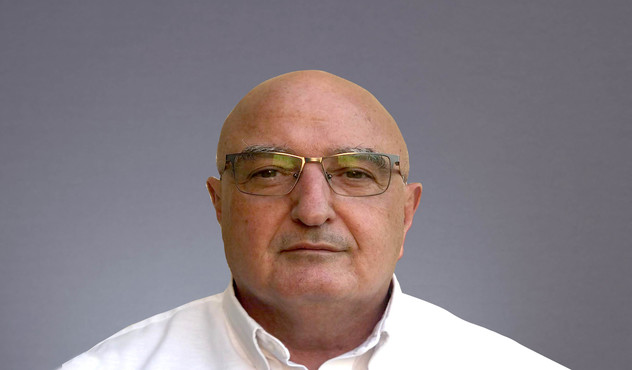
Managing Health & Safety
While managing our employees' health and safety is important in all our facilities around the world, it is especially crucial at our production sites, where the potential for accidents, exposure to hazardous materials, and erroneous use of equipment is higher than at other facilities.
Our sites are governed by localized HSE policies and guidelines. We are in the process of completing ISO certifications for all our sites with ISO 45001, 14001 certifications expected by the end of 2023.
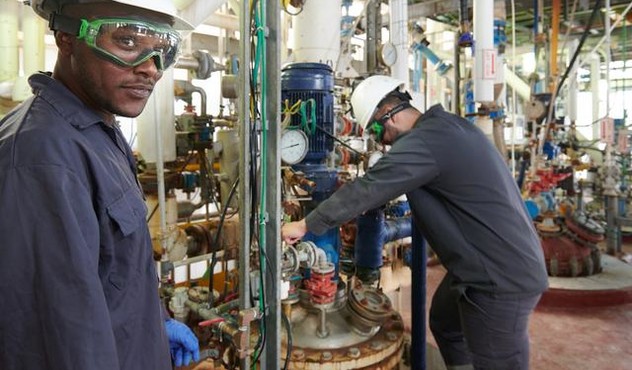
Global H&S Processes
In 2021, we continued to build our global safety processes, by:
- Reporting according to Syngenta Group standards
- Building the overall HSE model and system
- Recording 213 events, of which 179 were low severity and near miss
- Managing Covid-19 aspects across all global locations
- Building our process safety education program
- Training and certifying new process safety engineers
- Taking an active part in major safety projects
Our process safety is led by proactive Job Hazards and Process Safety Analysis (HAZOP, JSA, PSA) and is based on the 20 OSHA elements for assessment, which are followed closely and documented.
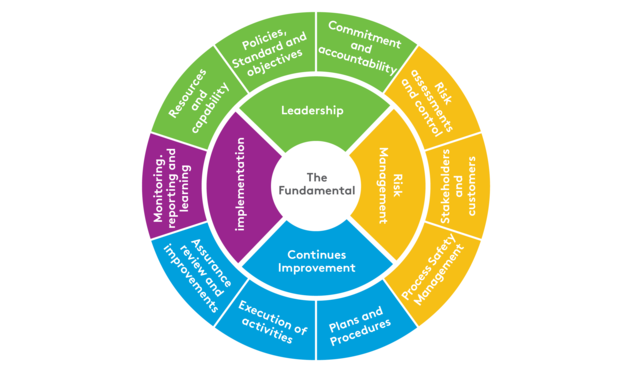
Monitoring and Assessing
We measure and monitor all processes and perform in-depth analysis of each safety incident, so that we are better prepared to prevent recurrence.
ADAMA’s Global HSE team hosts monthly meetings with HSE managers from all our sites, and with all our senior management. These meetings provide the opportunity to discuss the current safety indicators’ status, and determine what steps we should take to strengthen and monitor their implementation. Additionally, we measure and publish monthly safety KPIs and reports. During 2021, we started a quarterly review meeting with our operational sites, and a monthly meeting with the Chinese site (due to its size).
Periodic tests are held to ensure the health of our employees. These may include blood and urine tests to help determine whether employees have been exposed to unsafe substance levels. In addition, we hold periodic tests at all our manufacturing plants, to determine the level of hazardous materials that may be present in each working area.
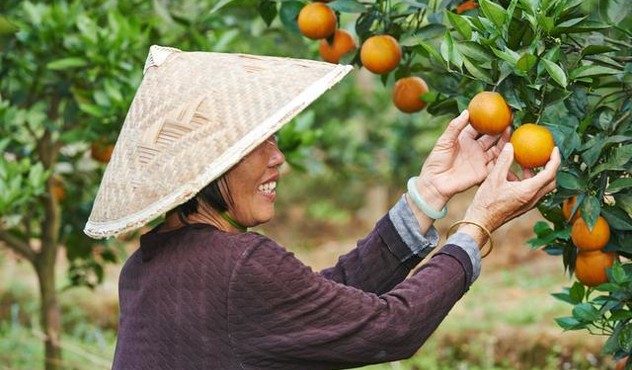
Analyzing H&S Risks
In recent years, we introduced a new management review process that includes root cause analysis. Besides analyzing the direct cause of incidents and their physical consequences, this analysis helps us identify their underlying roots – meaning, the source of the cause we need to tackle.
We conduct a safety monitoring process for all our sites, in accordance with a dedicated matrix that tracks their proactive safety activities with clear goals and KPIs. The sites report on an ongoing basis, according to this matrix and according to their size, with larger sites reporting more often than smaller ones. Sites are divided according to small sites with up to 100 employees, medium with 100-300 employees and large sites with over 300 employees.
The proactive safety activities matrix includes measuring and reporting on near miss and unsafe conditions, unsafe condition closure ratios, site manager tours, HSE personal safety tours, safety committees, training, exercises, and more.
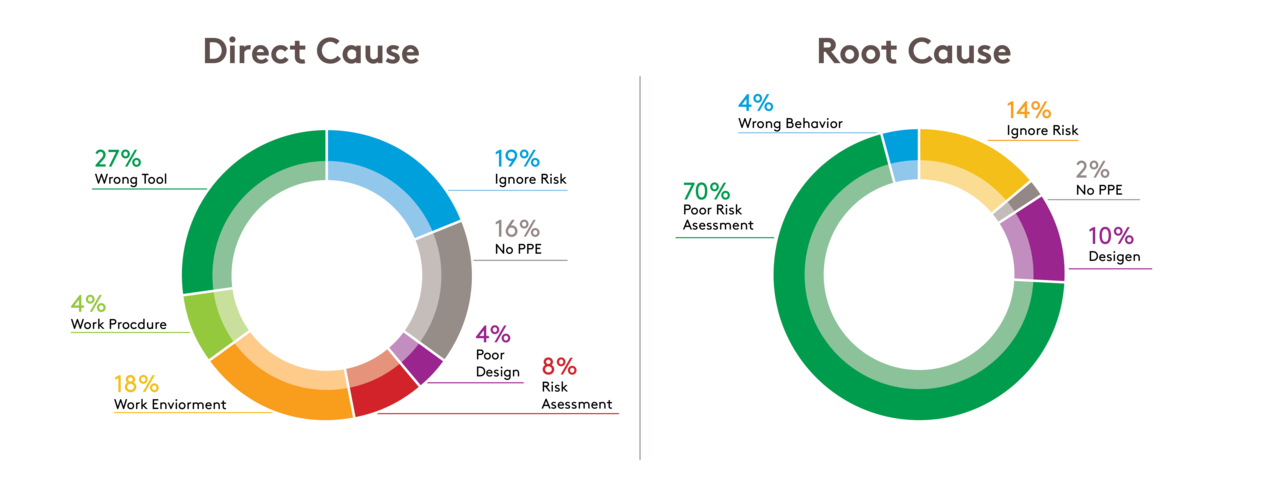
Developing H&S Culture
At ADAMA, we aim to build an incident-free work environment, in which safety is automatically integrated into business practices. We are already halfway to achieving our goal, and our main managerial focus is now concentrated on developing an organization-wide safety culture, which will influence all our employees’ behavior.
In 2019, we established our H&S model that outlines a 5-step path towards our desired outcome: From “Acting Safe” to “Being Safe.” All our sites have reached third step, or higher, of the process
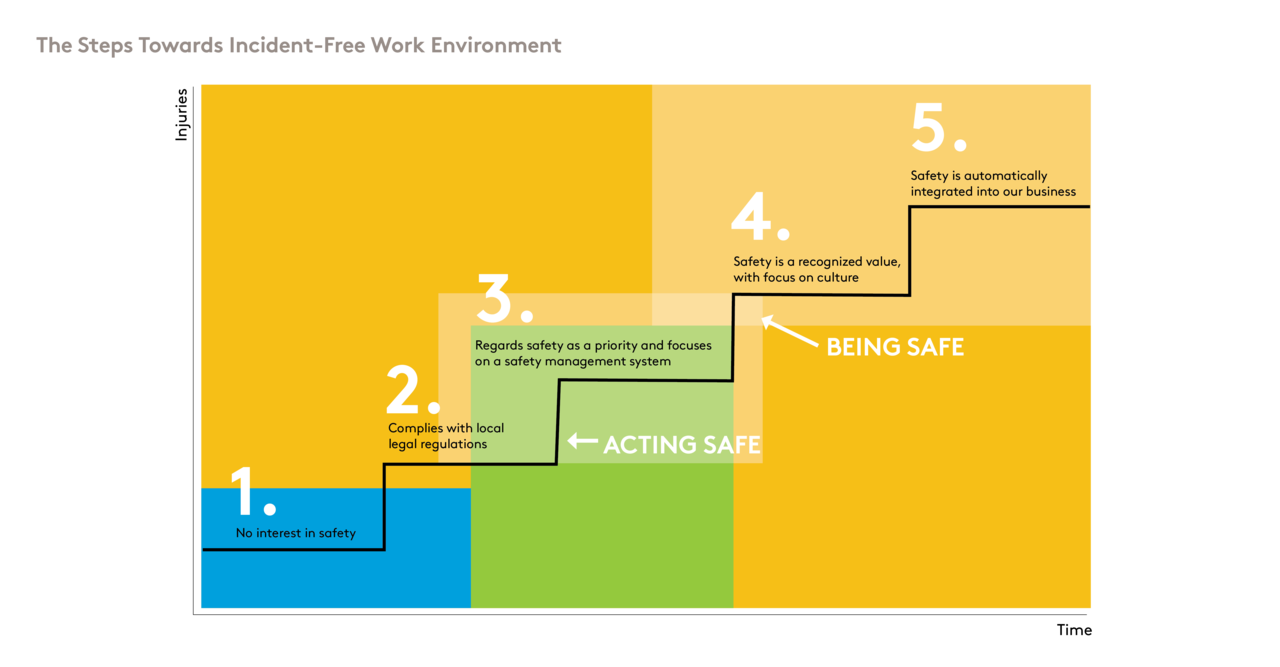
Health and Safety Commandments
To create a simple, unified H&S approach across our global sites, we have created our own “safety commandments.” Containing eleven clear and concise rules, the guide has been translated into the local languages, and is posted in a central location at all our facilities so that it is visible to all employees.
Aligning with Syngenta Group
During 2021, we finalized full integration to Syngenta Group life saving rules and communicated it cross the organization.
Training on HSE
Analyzing site safety challenges has led to employees taking greater care and thereby avoiding many accidents. Therefore, we invest a great deal of resources in training our employees and in prevention, including:
- Mandatory training for all employees - each employee must undergo a refresher training of one to two days, according to the site’s local regulations site.
- Local safety risks - all employees undergo annual training regarding the risks in their specific work environment.
- Dedicated training for emergency crews.
- Safety conversations - for managers and employees on the subject.
- Monthly enrichment sessions
- Communication regarding lessons learned post-accident – after each event in a one-pager to all company employees.
All sites measure, monitor and report back on the safety training they have undertaken.
Communicating About Safety - HSE Portal
To make communication about safety more accessible, we launched an HSE portal with all the relevant information, which is now available to all employees.
This information includes policies, updated global procedures, tutorials, and KPIs.
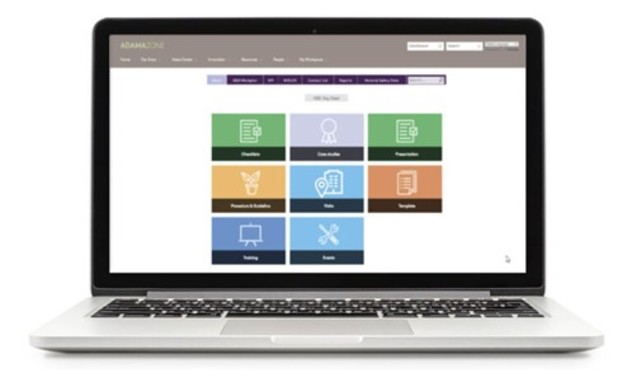
HSE Apps – ADAMA-Safe
To further ensure convenience in accessing the safety information, we have developed and launched an HSE app.
All our sites adopted local mobile applications that are used to report unsafe conditions, including assigning incidents to the responsible party, tracking progress, and handling the hazard.
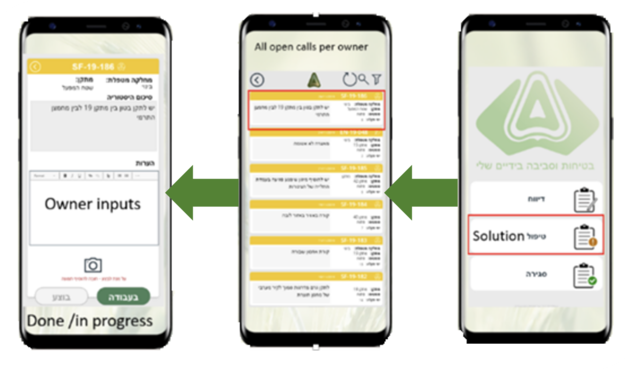
Injuries KPI
According to OSHA, there were 49 recordable injuries at ADAMA's sites in 2021. Although ADAMA increased its total number of employees during 2021 by opening a new site in China (an increase of about 30% in the total number of working hours), we were able to continue and show improvement in this KPI.
Most injuries (~60%) were cuts of various types, and there was a number of fractures. Unfortunately, we had two cases of severe cuts and one hip surgery. About 16% of accidents were related to exposure to chemicals (two from 2020).
During 2021, we had 1,744 missed days due to injuries, double that of 2020, due to three events that accounted for 833 sick days, and accidents from 2020 that continued into 2021.
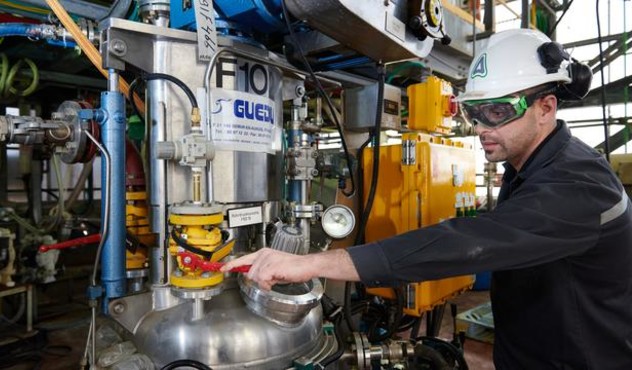
Five of our sites had ZERO injuries during the last three years - Poland, CSI, Tifton, Ocilla, and Mexico, and we encourage all our sites to follow their success.
It is important to emphasize that we treat all employees as equals, which is why the number of accidents includes permanent employees, contractor employees, and accidents on the way to and from work.
We achieved a continuous reduction of the injury rate since 2012, reaching 0.45 in 2021
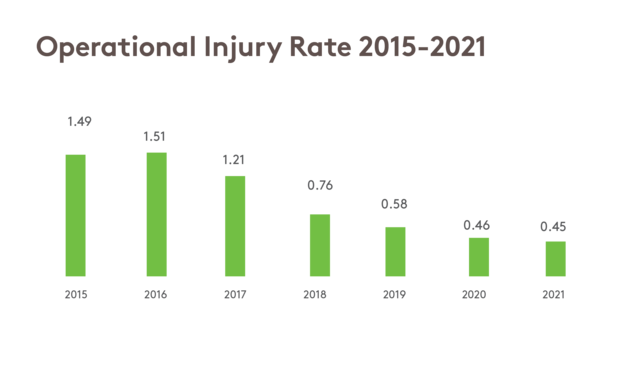
Managing Health and Safety During the COVID-19 Pandemic
The Covid-19 pandemic has forced us to formulate new mechanisms adapted to the new constraints, to continue to ensure the health and well-being of our workers in their homes. Therefore, we have established new guidelines and protocols, including implementing the following steps:
- Ongoing monitoring of the number of workers in isolation, active infections, etc.
We are sorry to report that we lost 10 employees to the COVID-19 pandemic. We investigated and we could not find that the infection took place on site. - ADAMA provided support to employees who fell ill due to COVID-19, including support for family members, delivery of medicines, ensuring hospitalization and the best local medical services, etc.
- ADAMA proactively donated oxygen machines to a local hospital in India, which serves the community close to our site there.
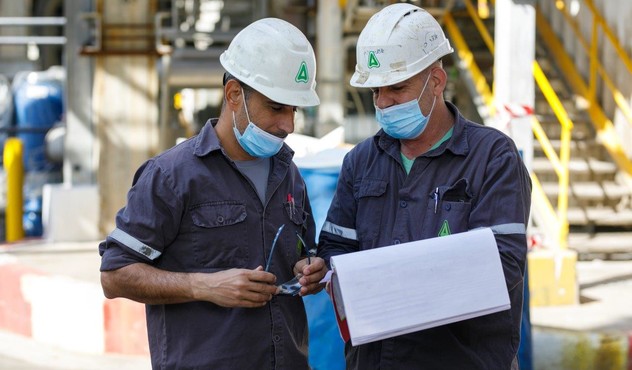